During World War II, an urgent need was felt for salvaging vessels sunk into the sea and this need raised the status of underwater welding from almost a pipe dream (pardon the pun) to a practical process.
Since then, underwater welding has been regularly used on ships for temporary repair work caused by collisions, unexpected accidents, corrosion and other maintenance works.
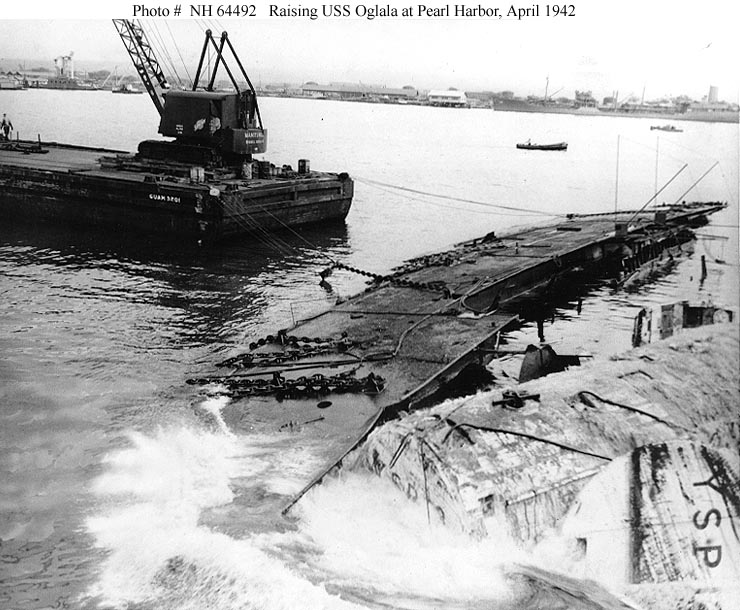
Over the past fifty years, international interests have further developed underwater welding, such as the construction of offshore gas and oil fields, fisheries, mines and wind farms.
Some underwater welding processes include deep water welding. Deep water work is never easy and the welder must be an experienced diver. Various welding positions can be challenging and diving operations are dependent on tide and weather.
Contents
Types of Underwater Welding
Underwater welding is split into two types of welding techniques: wet welding and dry welding.
Wet Welding
Wet welding is carried out directly in water using waterproof electrodes. Wet welded arc welds suffer hardness and brittleness as a result of the quenching effect of the surrounding water. Hydrogen released due to dissociation of water in the arc can also dissolve into the weld metal and lead to weld cracking.
An essential requirement for underwater welding is complete insulation. Even the electrode coatings are protected by a layer of wax, varnish or cellulose.
Advantages of wet welding are:
- Less expensive process than dry welding
- Faster set up, you can get to weld site quickly
- More freedom to move into restricted spaces
The most commonly used process of wet welding is Stick/SMAW.
Dry Welding
Dry Welding needs a pressurized enclosure with a controlled atmosphere. The weld metal is not in direct contact with any water. Dry welding produces very good welds, but the process is expensive.
Advantages of dry welding are:
- Reduced hydrogen interference in the environment
- Weld metal isn’t cooled by the surrounding water
- Weld strength and ductility comparable to surface welds.
The two main types of dry welding are hyperbaric welding and cavity welding.
Hyperbaric Welding (Habitat Welding)
Hyperbaric welding is carried out in a dry chamber constructed around the joint to be welded.
Water is expelled by providing a gaseous atmosphere in the chamber at pressure equal to water pressure and so keeping the water out.
This process is termed as habitat welding when used for joining large pipelines where the chamber is large, filled with a breathable atmosphere and equipped with a life support system for the operator.
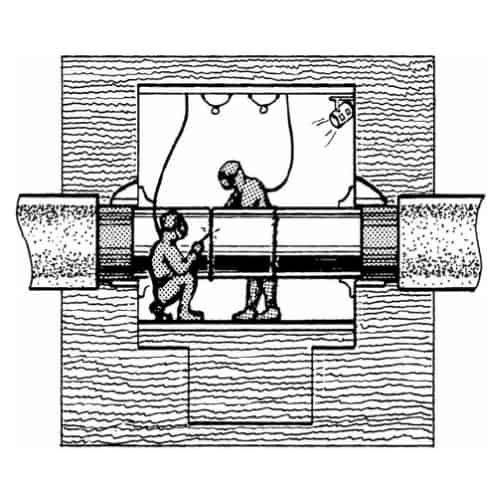
Hyperbaric process has certain limitations:
- The necessity for seals between the chamber and the structure to be welded is a practical difficulty.
- Increase in pressure as depth increases introduces problems both for the welding process and for divers. Weld chemistry, metallurgy and arc, physics are all affected.
Air as the habitat atmosphere soon becomes objectionable as pressure increases because it presents a potential fire hazard and oxygen becomes a narcotic. Air as an atmosphere is not recommended for depths above 15 metres.
Cavity Welding
Cavity welding is another approach to weld in a water free environment. In this process, the conventional arrangements for feeding wire and shielding gas are surrounded by a means for introducing cavity gas and the whole is surrounded by a trumpet shaped nozzle through which a high velocity water jet passes.
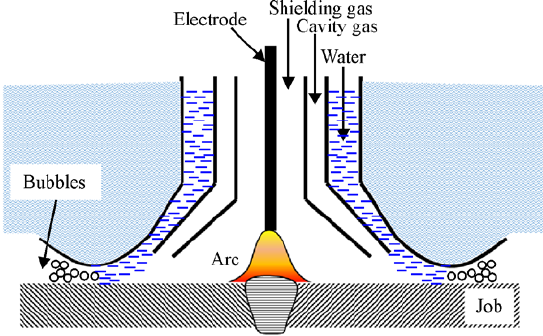
Cavity method avoids the need for a habitat chamber and it lends itself to automatic and remote control. The process is very suitable for flat structures where butt welds with a back up strip can be welded in the flat or overhead positions.
Cavity welding does not appear to be suitable for unbacked pipeline butt joints nor for lap joints which have accounted for the majority of underwater welding work
Stick Underwater Welding
Stick welding/SMAW is a commonly used, economical process for wet underwater welding. This process can be carried out in all positions with the same success as welding in air.
All electrical leads, lighting gear, electrode holder, gloves, etc must be fully insulated and in good condition. Ferritic electrodes with a coating based on iron oxide should be used as they resist hydrogen cracking.
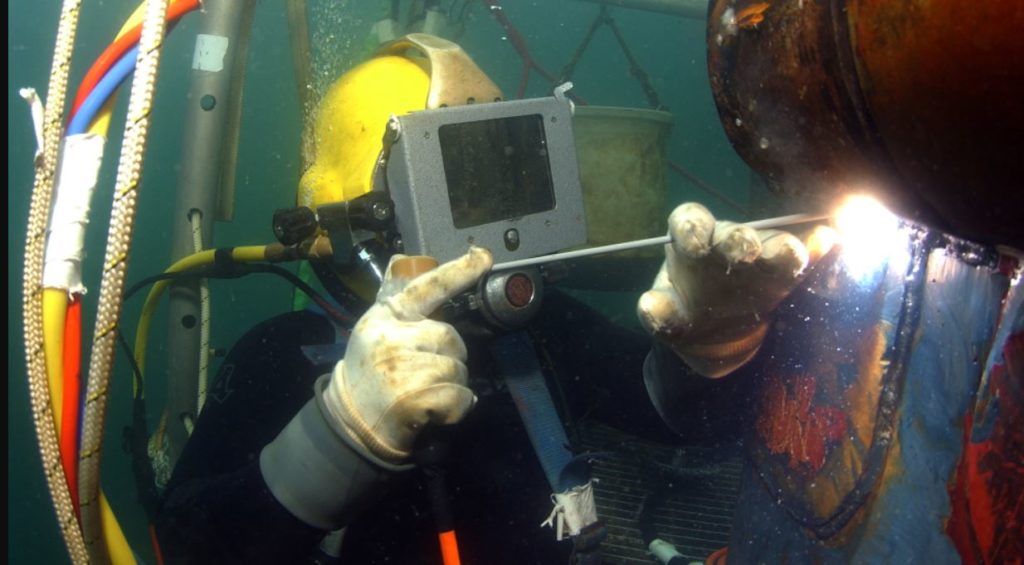
Welding polarity is always DC. DCEN is preferred in order to keep 65-75% of the heat in the metal being welded. DCEP may have to be used for overhead butt welding or welding cracks in the vertical and overhead positions.
Current settings for underwater welding are normally higher than for welding in air, and the control of these settings must be accurate to ensure consistent work. Generally, the greater the depth of the water, the higher must be the machine settings.
When preparing the job before welding, all edges to be welded should be rough ground to fit and all paint and loose scale should be removed.
For striking the arc, the electrode is held at an angle of about 35-45 degrees to the surface of the plate and its end is struck against the plate. After the arc has started, the electrode is held on the plate and pressure is exerted to keep it there.
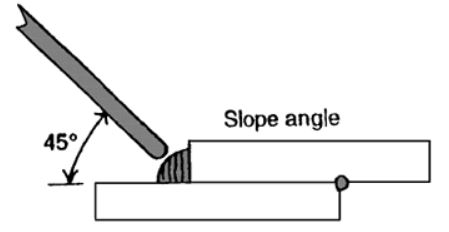
The arc length should be about the same as that for surface welding. The speed of welding, even in clear water, will be slower than the speed when welding is carried out at the surface.
The most common preparation for underwater welding is the fillet, which is, unfortunately, the more difficult of the joints to weld. Underwater fillet welds invariably require an oscillation, whereas underwater butt welds are rarely performed in this way.
The oscillation technique is achieved by raising and lowering the slope angle whilst welding. The oscillation occurs at the end of the electrode closest to the operator, so that the end closest to the workpiece remains a similar distance to the workpiece.
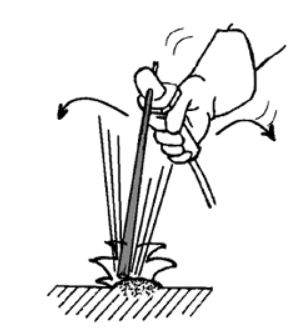
Slight oscillation of the electrode in this case gives more control over the weld pool and greatly assists the welder in producing a well shaped fillet.
TIG Underwater Welding
TIG welding/GTAW is widely used for dry underwater welding. Although this process is relatively slow, it has a number of advantages including being very flexible, accommodating variations in fit up and producing high quality penetration beads.
In TIG welding, as the depth and pressure increases:
- The Tungsten tip starts eroding which gives rise to arc instability and reduced penetration.
- Arc starting becomes more difficult. TIG welding becomes restricted.
MIG Underwater Welding
MIG welding/GMAW is a desirable dry welding process because of the high cost of diving operations. MIG welding is faster and less expensive than TIG welding and it can help to complete welds in the shortest possible time. This has directed attention to the use of semi automatic processes using solid wires or flux cored wires. Wires containing oxidizing and reducing elements give good results even without shielding gas.
MIG welding dry is preferred to MIG welding wet for better quality welds. You can MIG weld wet but stick welding is preferable for better results.
In MIG welding, as the depth and pressure increase:
- Arc heat increases and filler metal therefore melts faster as a result
- The shielding gas gets denser as pressure increases and may require flow rates up to 10 times the surface rates.
Applications of Underwater Welding
- Offshore construction for tapping sea resources.
- Temporary repair work caused by ship’s collisions or unexpected accidents.
- Salvaging vessels sunk in the sea.
- Repair and maintenance of ships.
- Construction of large ships beyond the capacity of existing docks.
- Welding of alloy steels can easily lead to embrittlement because of chilling effect of water on the weld metal. Under water welding is therefore generally restricted to mild steel.