Laser Beam Welding (LBW) commonly known as Laser Welding is a radiant energy welding process which joins materials together by the application of a concentrated light beam on the surfaces to be joined. Unlike electron beam welding it operates in air, no vacuum is required.
The laser concentrates light waves into a narrowly defined highly intense beam that can impart tremendous energy on a small area to produce strong fusion for welding.
Common light waves are incoherent and of varied lengths and frequencies that shoot off in numerous directions. The laser beam, on the other hand, is a coherent light i.e. the waves are identical and parallel.
Contents
How Laser Welding works
Ruby Crystal
The laser beam is produced by a man made cylindrical Ruby crystal. Ruby is aluminium oxide with chromium dispersed throughout it, forming about 1/2000 of the crystal, which is less than a natural ruby contains. The ends of the crystal are silvered to form mirrors internally, while one end has a tiny hole in the silver layer, through which the laser beam emerges.
Xenon Flash Tube
Around the outside of the crystal is placed a flash tube containing inert gas xenon. The flash tube is designed for operation of a rate of thousands of flashes per second and it converts electrical energy into light energy.
Capacitor Bank
The capacitor bank stores electrical energy. It is charged by a high voltage power supply. It energizes the flash tube by an appropriate triggering system.
Cooling System
Since most of the power output of a laser source is lost as heat, a cooling system is used. Both gas and liquid cooling are used, with liquid being more common.
Optical Cavity
The laser welding machine has an optical reflective cavity which reflects and focuses high-intensity radiation from the flash lamps onto the ruby (crystal) rod.
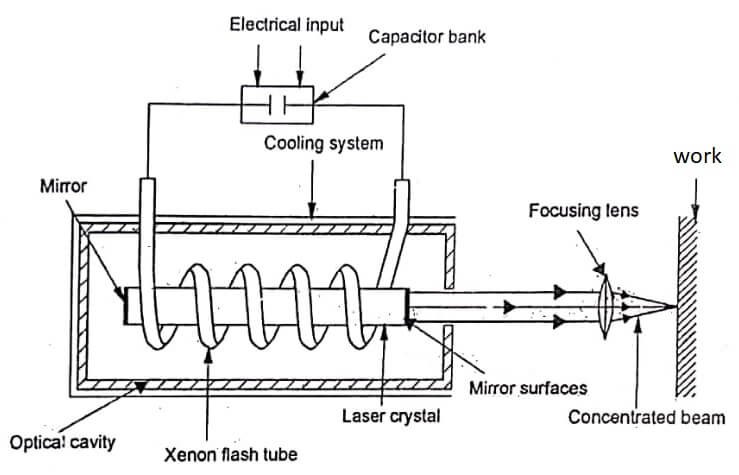
Step 1: When subjected to electrical discharge from the capacitors, xenon transforms a high proportion of the electrical energy into white light flashes. The flash has a duration of about 1/1000 second.
Step 2: As the ruby is exposed to the intense light flashes, the chromium atoms of the crystal are excited and pumped to a high energy level. These chromium atoms immediately drop to an intermediate energy level with the evolution of heat, and eventually drop back to their original state with the evolution of a discrete quantity of radiation in the form of red fluorescent light.
Step 3: As the red light emitted by one excited atom hits another excited atom, the second atom gives off red light which is in phase with the colliding red light wave. In other words, the red light from the first atom is amplified because more red light exactly like it is produced.
The effect is enhanced because the parallel ends of ruby rod are mirrored so that the red light that is produced reflects back and forth along the length of the crystal.
Step 4: The chain reaction collisions between waves of fluorescent red light and chromium atoms become so numerous that finally, the total energy bursts over a threshold and escapes from the small hole in the mirror at one end of the ruby crystal as the laser beam.
Step 5: This narrow laser beam is focused by an optical focusing lens to produce a small intense spot of laser (light) on the job. Optical energy as it impacts the workpiece is converted into heat energy. The temperatures generated can be made sufficient to melt (and vaporize) the materials to be welded or cut.
The minute puddle is melted and frozen in a matter of microseconds. Since this time is very short, no chemical reaction between the molten metal and atmosphere takes place and hence in laser welding no protection (shielding etc.) is needed against atmospheric contamination.
Applications of Laser Beam Welding
- Commonly used in automotive and aerospace manufacturing.
- Connecting leads on small electronic components and in integrated circuitry in the electronic industry.
- To weld lead wires having polyurethane insulation without removing the insulation. The laser evaporates the insulation and completes the weld.
- (To join hard high melting point metal alloys
- Laser welding is used in jewelry and medical industries with a smaller handheld laser welding machine
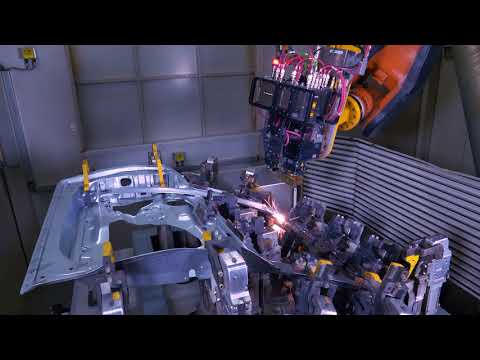
Advantages of Laser Welding
- A wide variety of materials can be welded, including some formerly considered as unweldable combinations. The material being welded need not be a conductor of electricity.
- As no electrode is used, electrode contamination or high electric current effects are eliminated.
- It permits welding of small, closely spaced components with welds as small as a few microns in diameter. it can be focused to microscopic dimensions and directed with great accuracy.
- Surface contaminants such as oxides and organic materials make little, if any, difference in the quality of the weld.
- Unlike electron beam welding, no vacuum is required.
- Laser beam being highly concentrated and narrowly defined produces narrow size of the heat affected zone.
- It is possible to weld heat treated alloys without affecting their heat-treated condition.
- Can be automated for high production rates
Disadvantages of Laser Beam Welding
- Cost of equipment and trained operators is high
- Materials such as magnesium tend to vaporize and produce severe surface voids.
- Depth of the weld is limited